伺服電機的定位原理核心是閉環反饋控制,通過 “指令 - 反饋 - 比較 - 調整” 的動態循環,實現對電機轉子位置的精確控制。其關鍵在于實時檢測電機實際位置,并與目標位置對比,通過持續修正驅動信號消除偏差,最終使電機穩定在目標位置。 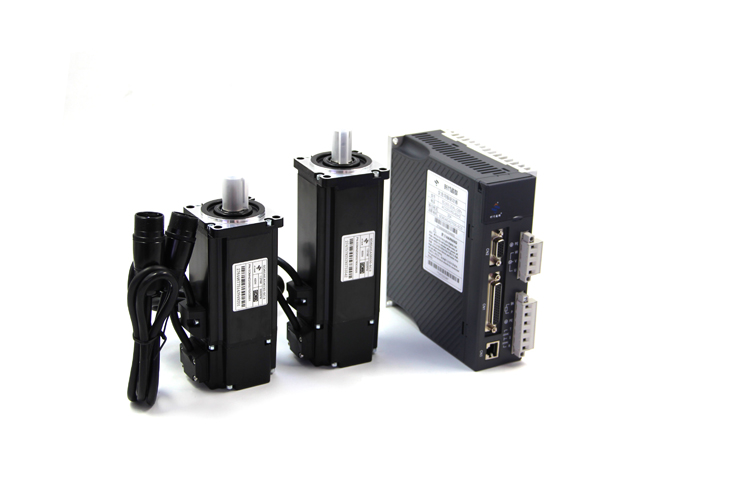
一、定位系統的核心組成伺服電機的定位功能依賴于 “電機本體 + 伺服驅動器 + 反饋裝置 + 上位控制器” 的協同工作,各部分作用如下:
電機本體:執行機構,將電能轉化為機械能(旋轉或直線運動),通常為永磁同步電機(主流)或直流伺服電機。 伺服驅動器:核心控制單元,接收上位指令、處理反饋信號、計算偏差并輸出驅動電流,控制電機運行。 反饋裝置:實時檢測電機實際位置 / 速度,最常用的是編碼器(如增量式編碼器),部分場景也用光柵尺、磁柵等。 上位控制器:發出目標位置指令(如 PLC、運動控制器、單片機),指令形式通常為脈沖數、模擬量或數字信號(如 Modbus)。 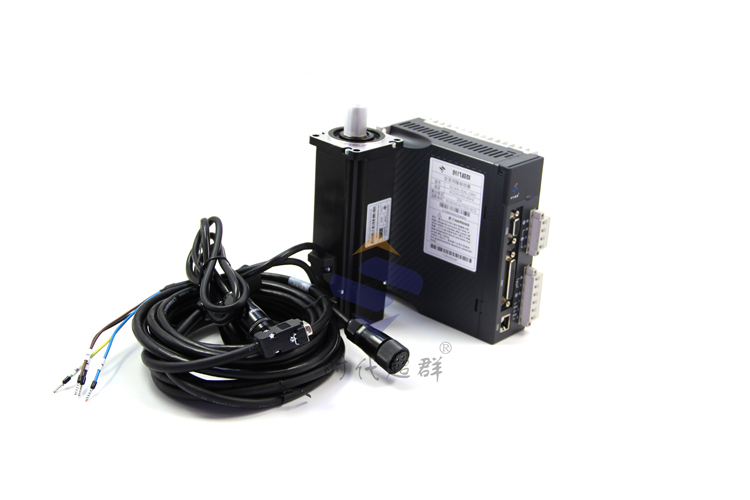
二、定位原理的關鍵環節伺服電機的定位過程是一個 “動態修正” 的閉環控制過程,可拆解為以下 4 個核心步驟: 1. 目標指令輸入上位控制器根據需求,向伺服驅動器發送目標位置指令。指令形式由通信方式決定:
脈沖指令:最常用,例如 “1000 個脈沖” 對應電機需轉動的角度(如編碼器每轉 10000 脈沖,1000 脈沖即對應 36°); 模擬量指令:通過 0-10V 電壓或 4-20mA 電流對應位置范圍(如 0V 對應 0°,10V 對應 360°); 數字指令:通過總線(如 EtherCAT、CANopen)直接發送位置數據(如 “目標位置 = 5000°”)。 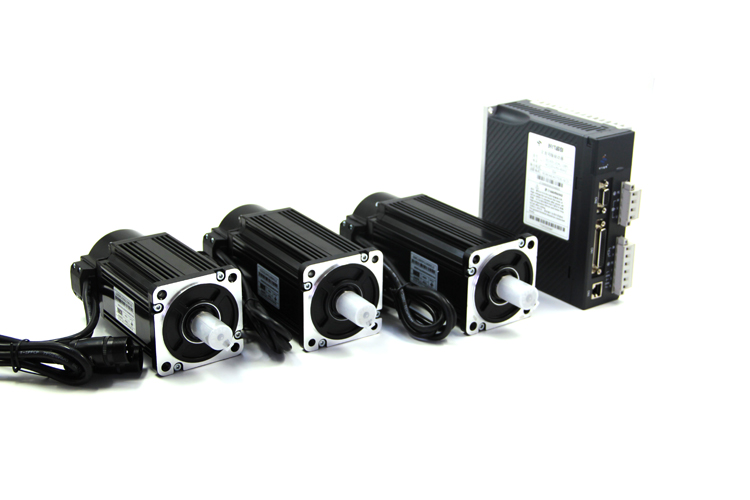
2. 實際位置反饋電機運行時,反饋裝置(編碼器)實時檢測轉子的實際位置,并將位置信號轉換為電信號(如脈沖、二進制編碼)反饋給伺服驅動器。
以編碼器為例: 增量式編碼器:每轉動一定角度輸出固定脈沖(如每轉 10000 脈沖),通過累計脈沖數計算相對位置(需配合原點校準);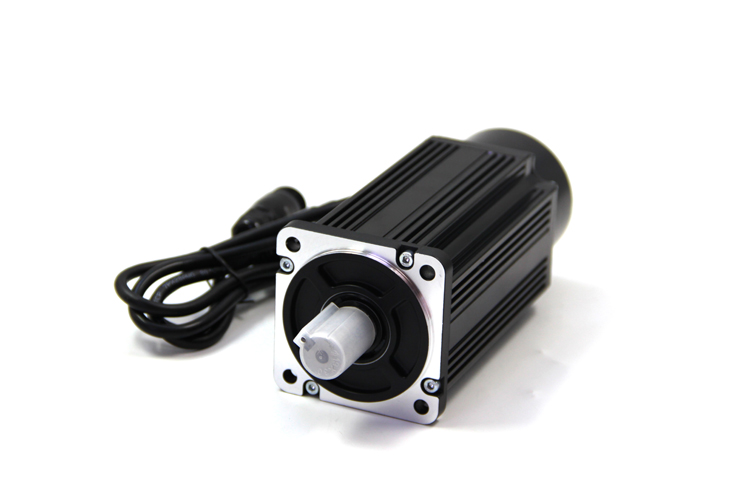 3. 偏差計算與控制算法伺服驅動器接收 “目標位置指令” 和 “實際位置反饋” 后,通過內部控制電路(通常為數字信號處理器 DSP)計算兩者的位置偏差(偏差 = 目標位置 - 實際位置)。
為快速、穩定地消除偏差,驅動器會采用PID 控制算法(比例 - 積分 - 微分控制):
比例(P):根據偏差大小直接輸出控制量(偏差越大,輸出越強),快速響應偏差; 積分(I):累計歷史偏差,消除靜態誤差(如摩擦導致的微小殘留偏差); 微分(D):根據偏差變化速度提前調整,避免超調(如電機沖到目標位置后反彈)。 4. 驅動調整與定位完成驅動器根據偏差計算結果,輸出相應的電壓 / 電流信號驅動電機轉動:
當偏差較大時,輸出大電流,電機快速加速,縮小偏差; 當偏差較小時,輸出小電流,電機減速,避免超調; 當偏差為 0(實際位置 = 目標位置)時,輸出電流為 0(或維持微小力矩防漂移),電機停止,完成定位。 三、定位精度的關鍵影響因素反饋裝置分辨率:編碼器每轉脈沖數越高(如 2500 線、10000 線),位置檢測越精細,定位精度越高(例如 10000 線編碼器,每脈沖對應 0.036°); 控制算法優化:PID 參數整定是否合理(如響應速度與穩定性的平衡),高端驅動器會加入前饋控制、模糊控制等優化動態性能; 電機特性:電機的轉動慣量、力矩輸出能力是否匹配負載,避免因負載過大導致 “拖不動” 或定位滯后; 機械傳動:若電機通過齒輪、絲杠等機構帶動負載,機械間隙(如齒輪咬合間隙)會直接影響最終定位精度,需配合消隙設計。
總結伺服電機的定位本質是 “閉環反饋下的偏差修正過程”:通過實時對比目標位置與實際位置,利用控制算法持續調整電機輸出,直至偏差為零。這一過程區別于步進電機的 “開環盲走”,因此能實現更高的定位精度(通常可達 ±0.01° 甚至更高),廣泛應用于數控機床、機器人、精密自動化設備等場景。 王工(13137008229)
|