基于ARM的印刷機高精度進墨控制系統(tǒng)基于ARM的印刷機高精度進墨控制系統(tǒng)
沈慧,陳佳品,李振波
(上海交通大學,上海200240)
摘要:隨著印刷行業(yè)的發(fā)展要求用于印刷機的進墨系統(tǒng)實現(xiàn)高精度定位。提出了進墨系統(tǒng)步進式的高精度控制.給出了該系統(tǒng)的機械結構、控制電路設計、上位機以及相關通信協(xié)議的設計。詳細介紹了步進控制實現(xiàn)的方法,并通過實驗得到3. 6。的精度,從而改進了舊設備的控制方法,達到了工業(yè)生產的需要,滿足了現(xiàn)代大型印刷的要求。
關鍵詞:進墨桿;電動機;上位機;步進運行方式;荸步精度
串圖分類號:TM381 文獻標識碼:A 文章編號:1004-7018(2010)01-0061-03
 0引言
隨著工業(yè)的發(fā)展,印刷行業(yè)所要求的色彩精度也達到了較高的水準。對于傳統(tǒng)的大型印刷機來說,進墨桿的定位精度對于整體印刷質量有著至關重要的作用。
進墨桿是控制印刷機進墨盒進墨量大小的關鍵設備。傳統(tǒng)的印刷機進墨系統(tǒng)采用到達位置電機剎車停止的方法,由于慣性的存在使得進墨桿定位不準,常常導致進墨過多、印刷質量下降的后果。
高精度定位的印刷機進墨桿直接決定了色彩精確性以及圖像的清晰度。由于傳統(tǒng)大型印刷設備的控制方法難以滿足高精度需求,本文利用近年來發(fā)展起來的ARM芯片[1]設計了一套適用于進墨系統(tǒng)的高精度步進方式控制系統(tǒng),使得原本難以預判的精度最終達到了3.6。的精度,從而達到了工業(yè)生產的需要。
1進墨控制系統(tǒng)簡介
進墨控制系統(tǒng)主要有進墨系統(tǒng)的機械結構、控制電路以及上位機組成。
1.1機械結構設計
進墨控制系統(tǒng)的機械結構主要由直流減速電動機、進墨桿、減速齒輪以及一個角度傳感器構成[2],如圖l所示。進墨控制系統(tǒng)的核心部件為進墨桿,進墨桿為螺線旋轉伸縮式:進墨桿伸縮長度的改變決定了進墨系統(tǒng)進墨量的大小。而進墨桿的伸縮民度又由直流減速電動機所決定,因此控制該減速電動機是控制該進墨桿的關鍵。在進墨桿的后方有一個手動調整進墨桿位置的部件,以便在進墨桿調試時使用。由于高精度步進電動機價格昂貴,并且在
機械結構改動方面存在一定困難,故本文采用直流減速電動機而不采用步進電動機。
1.2控制電路設計
進墨系統(tǒng)的控制電路主要由主控制模塊、測量反饋模塊及通訊模塊組成,如圖2所示。
主控制模塊由一塊ARM7內核PHLIPS的LPc2138微處理芯片[3],以及由橋路驅動芯片
TA8409構成的電機驅動電路構成。
PHLIPS公司生產的LPc2138微處理芯片具有64個引腳,31個雙向I/O口,2個8路10位A/D轉換器,能夠進行電壓測量的工作,符合設計要求,其引腳分配如表1所示。
主控模塊的主要功能是從通訊模塊接收到上位機傳來的通訊信息并加以處理,在完成一系列控制運算后,將止確的控制信息傳遞給減速電動機,從而控制電動機的旋轉,使得進墨桿得以運作。
測量反饋模塊主要由角度傳感器Mtdoi的cP一2FC以及相關AD采樣保持電路構成。m idori的cP一2Fc為360。機械角度電位器,它將機械角度位置信息轉化為電壓信號,并通過AD采樣保持電路傳回給主控模塊,其電路圖如圖3所示。
通訊模塊主要由一個支持Rs-422通訊標準的串口模塊組成:
1.3上位機軟件的開發(fā)
上位機軟件由基于Vc的MFc庫[4]編寫開發(fā)完成。在上位機的界斷中由設置區(qū)和數(shù)據(jù)回饋區(qū)兩部分組成。數(shù)據(jù)回饋區(qū)提供了數(shù)據(jù)回饋窗口,設置區(qū)主要用來設置步進步數(shù)等相關參數(shù)。整個上位機的串口通信由Microson commufllcation contml V6.O控件[5]進行控制,并在程序開始進行初始化串口,設定串口的通信模式。圖4為上位機程序編寫流程。
1.4 上位機與ARM控制電路通訊協(xié)議的設計
上位機實現(xiàn)對ARM控制電路的控制主要是通過傳發(fā)通訊信息完成的。在該系統(tǒng)中,通訊信息由 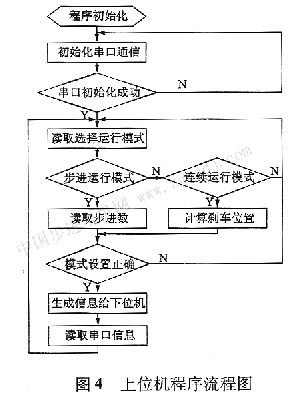
8個16進制的字符組成,這里值得一提的是通信信息并不是一個字節(jié)。如圖5所示,通訊信息的****位決定了電動機的運轉模式;低4位為電動機步進步數(shù),兇此該設計中電動機****步進步數(shù)為65 536步。
2進墨系統(tǒng)的控制方法
2 .1進墨系統(tǒng)的連續(xù)運行控制
進墨系統(tǒng)的連續(xù)運行控制原理簡單,只需在減速電動機上加上電壓即可。運行速度快是其主要優(yōu)點,但由于長期通電運行導致電動機在停機時存在慣性延遲的問題,因此在到達目標位置前需要提前計算剎車位置:這種計算不僅繁瑣,并且在不同的情況下,剎車位置的計算會出現(xiàn)偏差。因此這直接造成了連續(xù)運行的精度較低。在本文中,為了能使進墨桿快速到達指定工作位置,我們保留了連續(xù)運行方式,并將其作為粗調節(jié)方式使用。
2.2進墨系統(tǒng)的步進運行控制
為了實現(xiàn)更可靠的高精度定位系統(tǒng),我們設計了定步長的步進運行控制方式。
我們對高減速比的直流電動機進行控制,使它的運動方式由若干步等長的單步步進運行累加而成,因此單步步進的精度即為整個系統(tǒng)的精度。單步步進運行的精度由給定的控制方法中的延時時長所確定。系統(tǒng)電機的定位只需要計算出在整個步進運行控制方式下所需要走過單步步進的數(shù)量即可。
圖6給出了步進運行方式的控制流程。當上位機發(fā)送給ARM控制電路步進運行方式的指令后,ARM控制器將上位機發(fā)送來的指令信息從UATR口的緩沖區(qū)內讀人,并對它加以解碼,讀出包含在上位機發(fā)送指令中的步進步數(shù)信息,并將其放人寄存器中,同時將標志設最為步進運行模式。隨后,ARM控制電路打開電動機控制信號端口,給電機加電使其運轉。同時延時程序啟動,保持通電狀態(tài)。當延時時長結束時,電動機控制信號端口復位,電動機停止運轉,該過程完成了電動機步進運行方式中的單步運行。每當執(zhí)行完一次電動機單步運行過程中,存放步進步數(shù)的寄存器會從中減去1,當寄存器存放的值歸零時,整個步進運行方式也就此結束。
2.3單步步進的精度以及測定
從上述分析中可以發(fā)現(xiàn),電動機上電運行的延時時長決定了電動機單步步進的精度。我們在實驗中對于這種時常控制是通過設定延時程序中所需要執(zhí)行的延時循環(huán)的次數(shù)來實現(xiàn)的。
對于單步步進精度的測定,該控制系統(tǒng)中是由角度傳感器以及AD電壓保持電路所構成的測量反饋模塊共同完成的。
角度傳感器與進墨桿轉動比為1:2,并當角度傳感器旋轉一周即360。機械角度,其輸出電壓變化量為3 320 mv,當利用AD采樣測出單步步進后角度傳感器,然后根據(jù)下式便可測算出進墨桿步進角度。即:
式中:a為單步步進的精度;△U為通過AD采樣所得到的電壓差。
由于AD采樣在電動機完全停止后進行運作,因此保證AD采樣所采得的數(shù)值為準確值,沒有因為慣性作用而導致步進位置產生偏差。
3實驗數(shù)據(jù)以及數(shù)據(jù)分析
在實驗中電動機工作在單步步進狀態(tài)下,將電動機上電運行的時長設定為500個單位延遲時間,并且用我們的控制系統(tǒng)連續(xù)運行10個單步步進作業(yè),得出如表2所示的實驗數(shù)據(jù)。
從實驗數(shù)據(jù)中可以看出,當通電時間為500個單位延遲時,進墨系統(tǒng)的單步精度約為3.6。。在進行十步單步運行過程中,尊步運行的角度在3.57。~3 .63。,平均值為3.60。,均差為0.029。。可見,在實驗中依然存在著細微的偏差,但這些偏差一般是由機械結構的齒輪松動造成的,在實際生產運用中這些誤差在可接受范圍內。
4結語
本文設計了一個基于ARM核微處理器的進墨系統(tǒng)的連續(xù)與步進方式控制系統(tǒng),對控制系統(tǒng)的組成進行了闡述。就步進控制方法的實現(xiàn)進行了詳細描述,并且給出了基于這種步進控制方式下在實際實驗中所采得的數(shù)據(jù)以及分析。并且對適用于本設計的通訊信息格式以及上位機的編寫做了簡要的介紹。在本實驗中,通過介紹的控制方法,對直流減速電動機實現(xiàn)了單步步進的控制,最終定位精度達到了3.6。,從而實現(xiàn)了進墨系統(tǒng)的高精度控制。
|