自從1952年世界上第一臺三坐標數控銑床問世以來,數控機床的發展史至今已經有50余年的歷史。在這50余年中,數控機床技術得到了巨大的發展。從數控系統來看由以電子管為基礎的硬件數控技術發展到目前以微處理器和高性能伺服驅動單元為基礎的數控系統。伴隨著數控系統的發展,數控機床的伺服驅動技術也得到了相應的發展,從電液脈沖馬達、功率步進電動機發展到高性能交、直流伺服電機驅動系統。特別是高性能交流電動機伺服系統代表了當前伺服驅動系統的發展方向。數控機床控制系統作為機電控制系統的重要應用領域之一,從某種程度上也代表了當前機電控制系統的發展方向。 數控機床控制系統的組成如圖1.5所示。從圖中可以看出,數控機床的數控系統是由機床控制程序、計算機數字控制裝置、PLC、主軸控制系統及進給伺服控制系統等組成的。
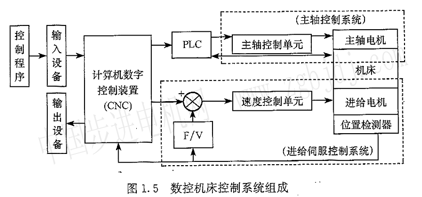 數控系統對機床的控制包含順序控制和數字控制兩個方面。順序控制是指對刀具交換、主軸調速、冷卻液開停、工作臺極限位置等一類開關量的控制;數字控制則用于機床進給傳動的伺服控制,以實現對工作臺或刀架的進給量、進給速度以及各軸間運動協調的控制。數控系統中,CNC裝置根據輸入零件加工程序,通過插補運算計算出理想的運動軌跡,然后輸出到進給伺服控制系統,加工出所需要的零件。另外,CNC裝置還完成對進給坐標控制、主軸控制、刀具控制、輔助控制等功能。其中,進給伺服控制系統是CNC和機床機械傳動部件間的聯系環節,是一個典型的閉環控制系統,它接收CNC的控制命令后,能夠平滑地調節運動速度,精確地進行位置控制。機床進給裝置的實際速度和位置通常由裝在電機軸上的速度和位置傳感器來檢測。 作為數控機床進給用的伺服驅動系統應滿足以下要求: (1)應具有足夠寬的調速范圍,通常要達到10 000:1以上才能滿足低速加工和高速返回的要求。 (2)應具有足夠的加(減)速力矩。為了快速移動機床導板或重切削的需要.要求伺服電動機能產生出足夠大的力矩。 (3)伺服驅動系統的動態響應要快,以使系統具有良好的動態跟隨性能,盡快消除負載擾動對電動機速度的影晌。 (4)伺服電動機的轉子慣量要小,以提高伺服系統的加(減)速性能,整個 電動機的質量和體積應盡可能小些,為機械設計與安裝創造方便的條件。 (5)在從低速到高速的整個速度范圍內,應該保持運行平滑;電動機的轉矩脈動盡可能要;在運行中不產生脈動和過大的噪聲;在停止時不產生爬行現象和高頻振動。 (6)伺服電動機應安全可靠,希望電動機本身無需維護或容易維護。這一點在使用多臺伺服電動機的生產線中是應該特別強調的。同時,也要求伺服電動機能在油氣、粉塵等易燃易爆以及人體無法直接接近等惡劣環境中正常工作。 (7)cNc系統的接口應當簡便。整個伺服驅動裝置必須能方便地接收來自上一級控制的指令,同時也必須將自身的運行狀態送到上~級控制器。這樣,在伺服電動機和伺服驅動器、計算機數字控制系統之間.存在著信號形式與強弱的顯著差別,必須通過接口聯系起來,這就要求接口應該是簡便易行的。 機床進給伺服控制裝置的負載在相當寬的范圍內具有恒轉矩的性質,而且負載慣量變化很小。從這個角度來看對控制系統的設計是有利的。但由于數控機床用于精密機械零件的加工,所以對進給系統的動態和靜態控制精度要求非常嚴格。 2. 機器人控制系統
現代機器人技術經過幾十年的發展,已經在各個領域得到了應用,特別是在工業生產中得到普遍應用。工業機器人是一個涉及多種技術的典型機電一體化產品。它廣泛用于汽車制造、機械加工、電子、能源、建筑以及軍工和海洋等工業部門·主要從事噴漆、焊接、裝配、搬運以及一些特殊環境下的工作,成為生產線的主要組成部分,而備受重視。工業機器人控制系統的構成如圖1.6所示。
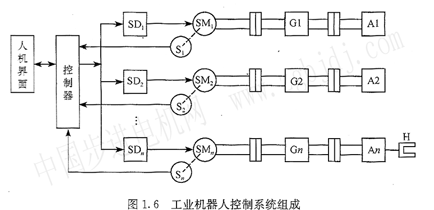 圖1·6中,機器人控制器相當于人的大腦,是工業機器人的重要組成部分,它支配著工業機器人按規定的程序運動,并記憶人們給以工業機器人的指令信息(如動作順序、運動軌跡、運動速度及時間等),同時按其控制系統的信息對伺服 驅動系統發出動作命令。為了能快速精確地控制機器各個伺服驅動軸的動作和位置,要求控制器能進行高速且復雜的坐標變換運算?刂破鞯暮诵牟考歉咝阅芪⑻幩倨鳎瑸榱吮阌诓僮髡呤褂,大多數工業機器人控制程序采用容易掌握的工業機器人專用語言。 伺服驅動器(sD)用來驅動伺服電動機。工業機器人控制器發出臂(或手爪)的速度指令信號與測量出的實際速度信號相比較,比較后的差值加到伺服放大器的輸入端,經過功率放大后控制伺服電動機轉矩和旋轉速度,使各臂平滑而快速地移動到預定位置。 伺服電動機(sM)作為工業機器人手和腰的驅動執行元件,要求體積小、質量輕,且能產生大轉矩。目前在工業上使用的大多數機器人,是模擬人體手臂動作的一種裝置,要求伺服電動機安裝在各臂的軸上,驅動各臂快速平滑移動。 為了減輕手臂的總體質量,希望采用高性能稀土永磁伺服電動機。目前,在工業機器人伺服驅動技術中,最常用的是Dc伺服電動機(直流伺服電動機)和Ac伺服電動機(交流伺服電動機)兩種,而Ac伺服電動機的應用越來越廣,并將取代Dc伺服電動機。 圖1.6中的傳感器(s),是指安裝在伺服電動機軸非負載端的速度與位置檢測元件,用它來檢測伺服電動機的轉速及轉角,從而進行各軸的速度與位置控制。常用的傳感器有光電編碼器、精密電位器等。這些傳感器和電子技術相結合,才使得伺服電動機的控制技術得到了迅速的發展,實現高精度的速度與位置控制成為可能。 工業機器人的手爪(H)是用來抓取物件的。工業機器人是一種典型的機電一體化產品,其驅動部分最常用的是電氣伺服系統,這種電氣伺服系統能忠實地跟蹤控制命令,得到優良的控制品質。 概括地說,工業機器人對伺服驅動系統的要求如下: (1)伺服驅動系統應具有足夠的輸出力矩和功率,以滿足各種條件下的工作需求。 (2)能夠進行頻繁的啟、制動和正、反轉切換等重復運行。 (3)能夠靈活方便地接受控制器的控制指令,實現轉矩、速度及位置控制。 (4)伺服系統應具有良好的穩定性,并能對控制命令進行快速響應。 (5)運動部件的慣量要盡可能小些。 (6)從整體上要求裝置的體積小、質量輕。 (7)便于維護。 從工業機器人驅動技術的發展歷史和不同的應用場合來看,驅動源有電氣式、氣壓式和液壓式等3類。其中電氣式伺服驅動容易獲得能源,干凈無污染,容易調節和變換,具有良好的控制靈活性。隨著微電子技術、電力電子技術和特種電動機材料技術的進步,使電氣式伺服驅動方式得到了越來越廣泛的應用。
3.現代交通運輸工具現代交通運輸工具已經走出純機械的模式,向著機電一體化的高性能綜合方向發展。如飛行器、電力機車、新型汽車等,這些系統都是高機動性的復雜機電系統,往往都是由若于個子系統組成并協調工作。下面以汽車防抱死制動為例作簡要說明。 眾所周知,汽車是陸地行駛車輛中機動性極強的交通工具,它既可行駛在高附著系數的干燥路面,也能行駛于雨、雪氣候條件下的濕滑路面。防抱死制動(anti-lock brake system,ABS)系統,是基于汽車輪胎與路面之間附著性能隨滑移率改變的基本原理而開發的高技術制動系統,它從防止制動過程中車輪‘‘抱死”的機理出發·避免汽車后輪側滑和前輪喪失轉向能力,以達到提高整個汽車行駛穩定性、操縱性和制動安全性的目的。此項技術的研究開發,從1932年第一個英國防滑專利U.K382241開始,至今已有半個多世紀的歷史。曾先后在火車、飛機的機輪剎車和汽車上使用,但成功地在汽車上推廣應用還是20世紀90年代初期的事情。目前,汽車ABS系統已經經歷了各種嚴酷條件下的可靠性檢驗和性能價格比方面的市場的考驗。實踐證明它具有如下顯著的優點: (1)防止汽車側滑甩尾,大大提高車輛制動過程中的方向穩定性。 (2)使汽車轉向輪具有可操縱性,即使在制動過程中,仍然能夠操縱汽車躲避開車輛前方的障礙。 (3)可縮短制動距離,特別是在冰雪路面上可以縮短制動距離約10%~20%。 (4)防止輪胎“拖胎”,減少輪胎磨損,減少輪胎粉末對大氣的污染,并可提高輪胎使用壽命6%~10%。 (5)提高汽車行駛的平均車速約15%。 汽車ABs系統如圖1.7所示,它由制動腳踏板1.、報警燈2、ABs的電子控
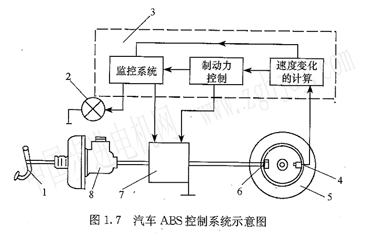
制單元3、輪速傳感器4、車輪5、制動分泵6、制動壓力調節裝置7和制動總泵S等組成。 ABS的工作原理是:電子控制單元(ECU)根據輪速傳感器和估計的車速計算車輪的滑移率和車輪的角加速度,然后將這兩個參數與相應的門限比較。當有抱死的傾向時,操縱制動壓力調節裝置減少制動壓力;當車輪的角加速度超過加速門限(或角減速度小于減速門限)時,操縱制動壓力調節裝置加大制動壓力;當處于兩者之間時,切斷分泵與主泵的聯系進行保壓。制動壓力調節裝置可以是一個三位三通電磁閥或兩個二位二通電磁閥換向閥。 4. 自動化制造系統(生產線)大規模制造的現代生產模式極大地推動了現代制造裝備技術的發展,出現了各種形式的自動化制造系統及裝備。例如,柔性制造系統(FMs)、計算機輔助設計/制造系統(CAD/cAM)、計算機輔助設計工藝(CAPP)和計算機集成制造系統(cIMs)以及各種工業過程控制系統。在這些系統中,也可能包括若干個前面提及的像數控機床、工業機器人等較復雜的機電子系統。 自動化生產制造系統根據作業工藝流程,可分為連續型制造過程和離散型制造過程兩大類。連續型制造過程系統的控制以過程量為控制特征,如溫度、壓力、流量等,這類制造系統主要應用于石油、化工、冶金、能源等生產領域;離散型制造過程則主要出現在機械制造和電子制造領域,其主要的控制特征是邏輯控制和運動控制。然而,隨著技術的發展和生產要求的提高,連續型制造過程和離散型制造過程相互滲透,出現了所謂的混合控制系統。 在離散型制造過程自動化制造系統中,****代表性的就是自動化組裝(或裝配)系統,極大多數系統根據工藝過程按線形分布,所以有時也稱其為自動生產線。
|