摘要:為了實現電磁體摩擦表面均勻磨損和抗旋轉趨勢,從電磁制動器制動機理出發,分析了電磁體制動時的工作姿態及其表面磨損情況,提出內側磁路開槽的非對稱設計方法;并利用Ⅱ3D有限元軟件仿真優化得到****的電磁體非對稱結構參數;最后給出對稱結構和自主優化設計的非對稱結構電磁體磨損對比試驗,驗證了理論分析的正確性和設計方法優越性。 關鍵詞:制動器;電磁體;非對稱;磨損;優化設計引 言傳統的車輛制動器主要采用液壓制動和氣壓制動,由于封閉性不強導致泄漏使車輛制動器制動效能不良。電磁制動器是一種由電磁吸力產生制動力的新型鼓式制動器,采用電流方式控制制動力大小。其核心部件是電磁體。電磁體性能好壞直接關系到電磁制動器制動性能和可靠性。國內外在針對電磁體結構與性能方面作了許多研究工作,如電磁體形狀改變,電磁體前后非對稱設計,以有效克服傾覆。這些研究使得電磁制動器取得長足發展并很快進入實用階段,但其也存在諸多不足,尤其關鍵部件電磁體的旋轉傾向和不均勻磨損使得電磁體壽命大大縮短。本文在理論分析的基礎上,提出內側磁路開槽的非對稱設計方法,利用電磁場有限元分析軟件得出非對稱結構電磁體的結構參數。試驗驗證表明該方法可以實現電磁體摩擦表面的均勻磨損和抗旋轉趨勢。 電磁制動器結構及運行機理鼓式電磁制動器的結構由電磁體l、制動蹄片、制動杠桿3、銷軸4以及回位彈簧5等組成,如圖1所示。車輛制動時,電磁體由控制器輸入電信號產生電磁吸力,電磁吸力使之與制動鼓端面外側吸合,形成閉合磁路,車輪的轉動帶動電磁體隨動,與電磁體十字聯接的制動杠桿長臂繞支點帶動短臂產生位移,短臂頂開制動蹄片,實現制動;制動結束后,電磁體斷電,回位彈簧使之回到初始狀態,制動蹄片松開。在制動過程中.制動蹄片移動到位后,車輪仍在(減速)旋轉。醫此制動鼓端面外側與電磁體有相對摩擦,電磁吸力轉換成的摩擦力決定了制動力的大小。
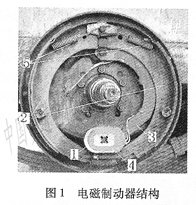
2.電磁制動器優化設計
由電磁制動器運行機理可知,制動時電磁體以制動鼓端面中心為圓心作圓周相對滑動摩擦。 如圖2所示,0為制動鼓端面的旋轉圓心,R1、分別為電磁體內、外側到圓心0的等效距離。如果磁路關于長軸對稱,則電磁體內、外側相同的等效摩擦力將導致以下一些問題: 首先,電磁體內、外側因離圓心0的等效距離不同而導致線速度不同,如果摩擦面內、外側吸力相同,則磨損速度因外側線速度大而比內側快,影響電磁體壽命。 其次,從電磁體摩擦面上各面積元來看,其受力方向與制動鼓端面在該處運動的切線方向相同,因此電磁體受到使之與制動鼓轉動方向一致的旋轉力矩。warnnel電磁制動器公司采用活動十字聯結的機械結構,以防止電磁體本身的旋轉趨勢,但過大的旋轉力矩在制動過程中容易卡住聯結處,從而影響制動的可靠性。 采用內側磁路開槽的非對稱設計方法,使制動時對應的摩擦力內側大于外側,不僅可以達到均勻磨損目的,而且產生一個與因制動鼓旋轉使電磁體產生旋轉趨勢的反向力矩,從而減小了電磁體的旋轉傾向,防止了聯結處卡死而引起抖動及噪聲,使制動器工作更平穩,制動更安全。 3.基于Ansft/Maxwell 3D的電磁體優化計算
在理論分析中采取內側磁路開槽的方法,使電磁體工作時內側電磁吸力大于外側電磁吸力。 槽深在理論上開得越淺越好,但電磁體磨損試驗數據顯示,在要求制動的5萬公里條件下,電磁體****處磨損量為1.:382 mm。考慮一定的安全系數和制造工藝,把槽深定為2 mm。在此基礎上,通過電磁場分析軟件Ansoff/MaxweII 3D得到電磁體的開槽面積、開槽數兩個結構參數。
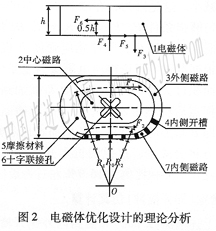 3.1開槽面積百分比的仿真優化面積大小對電磁體的吸力大小影響很大。首先分析開槽面積對電磁體工作的影響。對電磁體不同的內外側面積比進行仿真,仿真數據見表1。 開槽面積比與電磁吸力的關系曲線(圖3)和開槽面積比為16.7%的電磁體的B矢量云圖見圖3和圖4。
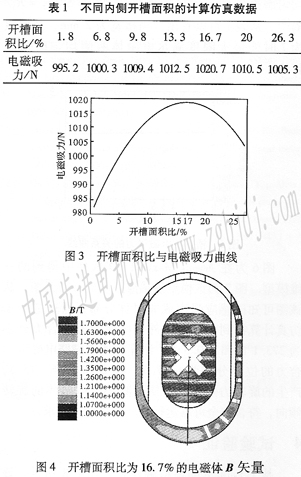 開槽面積比由O逐漸增加,電磁吸力也逐漸增加,但是當開槽面積比達到16.7%左右時電磁吸 力達到峰值,隨后電磁吸力隨著開槽面積的增加而逐漸減小。這是因為,在磁通φ一定的條件下,根據均勻磨損條件F2/F1=SI/s2=R1/R2可知,當內側磁路面積減少,則磁感應強度B也同比例增加,根據電磁場理論得出電磁吸力也是增加的;當開槽面積過大時,磁感應強度B增加到磁化益線的膝拐點后將不再明顯增加,而開槽面積繼續增加,即B增加的幅度低于開槽面積比的幅度時,電磁吸力將會減少,這說明再多開槽效果已不明顯,因此開槽面積比例為16.7%左右為****。 3.2槽寬(即開槽數)仿真計算
以上述槽深(2 mm)和磁路內外側開槽面積比為16.7%,仿真計算槽寬(即開槽面積/開槽數)對電磁體吸力大小和分布的影響(考慮到磁路結構特性和摩擦均勻性,采取均勻開禧的方式)。槽寬與電磁吸力的關系曲線如圖5所示。可知,槽寬對電磁吸力的影響很小,但對電磁體吸力的分布有較大影響。通過Anson/Maxwell 3D有限元軟件,得到內外側磁路產生的電磁吸力計算數據。為滿足均勻磨損條件均勻磨損條件F2/F1:s1/s2=R1/,從表1可以看出,當槽寬為2 mm、開槽數為7時能****限度滿足電磁體兩側均勻磨損之目的。
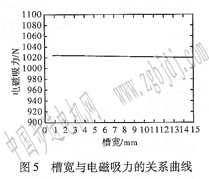 圖6為在Ans0ftMaxwell 3D軟件中得到的三維模型。圖7為該模型磁感應強度的分布云圖。從該圖可知磁感應強度成非對稱分布,通過進一步仿真計算得到電磁體內外側電磁吸力的合力分別為273.1 N和240.3 N,計算內外側磁路電磁吸力合力的位置分別為一17.5,14.2和17.6,15.5,產生的旋轉力矩很小,從而減小了電磁體的旋轉傾向。符合安全可靠運行的非對稱設計要求。 4. 試驗驗證
基于lablive的虛擬測控裝置如圖8所示 。該裝置時自行研制的生產線用電磁體性能測試臺。 以調速機帶動鐵盤旋轉,電磁體吸合在轉盤上,產生相對摩擦力.模擬不同車速時的制動鼓端面吸合和電磁制動器實際制動過程。各種傳感器可測定電磁體的電壓、電流、溫度、靜態與動態電磁吸力及不同車速下的制動力(等效成動態摩擦力),還可以設置電磁體通電間隔,模擬多次重復制動工況,作電磁體工作姿態穩定性、磨損性及壽命試驗。
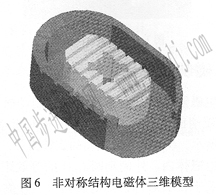 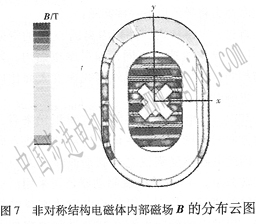
在自制的制動實驗臺上作磨損試驗。計算機設置電磁體加額定電壓為12 V,與摩擦盤吸合模擬一次制動試驗,自動重復該動作,歷時4天,對非開槽和開槽的電磁體分別進行7 000次的制動試驗。非開槽電磁體內外側磨損差異為0.07 mm, 而自主優化設計的非對稱內側開槽電磁體內外側磨損差異為O.02 mm,而且克服了制動時的抖動現象,噪聲更小,工作更平穩。可見,自主優化設計的內側開槽的非對稱結構電磁體,不但提高了制動安全性,而且減小了磨損,延長了電磁體的使用壽命。 5.結論
本文提出一種新的非對稱結構電磁體設計方法,用在電磁體內側磁路開槽的方式來實現非軸對稱設計,改善了電磁體內外側磨損均勻性,從而避免了電磁體由于夕}側磨損快使線圈外露而報廢的問題,延長了制動器的工作壽命,并提高了可靠性,同時擴大了線圈的可置繞線空間,克服了重心偏移于十字聯結處的缺點,減小了電磁體的旋轉傾向,防止聯結處卡死而引起的抖動及噪聲,使制動器工作更平穩,制動更安全。研究成果已用于產業化應用和項目鑒定中,并獲得了發明專利受理,為研制不同系列電磁體打下了基礎。
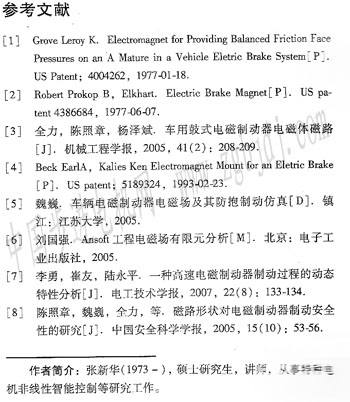
|